The rise of e-commerce has dramatically transformed the retail landscape, but its impact extends far beyond just changing how consumers shop. One of the most significant ripple effects is the growing importance of reverse logistics – the process of managing returns and exchanges. As online shopping continues to boom, the demand for efficient reverse logistics operations is set to drive a surge in warehouse and distribution center (DC) requirements.
The Growing Returns Challenge
Online purchases have a much higher return rate compared to in-store purchases, often ranging from 15% to 40% depending on the product category. This creates a massive volume of items that need to be processed, inspected, refurbished, and reintegrated into inventory or disposed of properly.
Traditional warehouse designs and processes were primarily focused on outbound logistics. Now, companies are scrambling to adapt their facilities and operations to handle a bi-directional flow of goods efficiently.
Impact on Real Estate Demand
This shift is having a profound effect on industrial real estate:
- Increased Space Requirements: Processing returns requires additional space for sorting, inspecting, and repackaging. Many retailers are finding their current facilities inadequate to handle the volume.
- Strategic Locations: To minimize shipping costs and speed up the returns process, companies are seeking warehouse locations closer to urban centers and transportation hubs.
- Specialized Facilities: Some businesses are opting for dedicated returns processing centers, creating demand for purpose-built facilities with features like enhanced sorting areas and refurbishment stations.
Technology Integration: Modern reverse logistics operations rely heavily on advanced technology, driving demand for “smart” warehouses with robust IT infrastructure.
The Opportunity for Investors and Developers
The reverse logistics trend presents a significant opportunity for industrial real estate investors and developers:
- New Construction: There’s growing demand for state-of-the-art facilities designed specifically with reverse logistics in mind.
- Retrofitting: Existing warehouses and DCs may need substantial upgrades to accommodate reverse logistics operations efficiently.
- Urban Infill: The need for facilities closer to population centers could drive redevelopment of older industrial properties in strategic urban locations.
Looking Ahead
As e-commerce continues to grow and consumers become increasingly comfortable with liberal return policies, the importance of reverse logistics will only increase. Forward-thinking retailers, logistics providers, and real estate developers who position themselves to meet this growing need are likely to find themselves well-positioned in the evolving retail landscape.
The surge in warehouse and DC demand driven by reverse logistics is not just a short-term trend, but a fundamental shift in how supply chains operate in the digital age. Those who adapt quickly and efficiently to this new reality will likely find themselves with a significant competitive advantage in the years to come.
The impact of reverse logistics on real estate demand is multifaceted and significant. Here’s a more detailed breakdown:
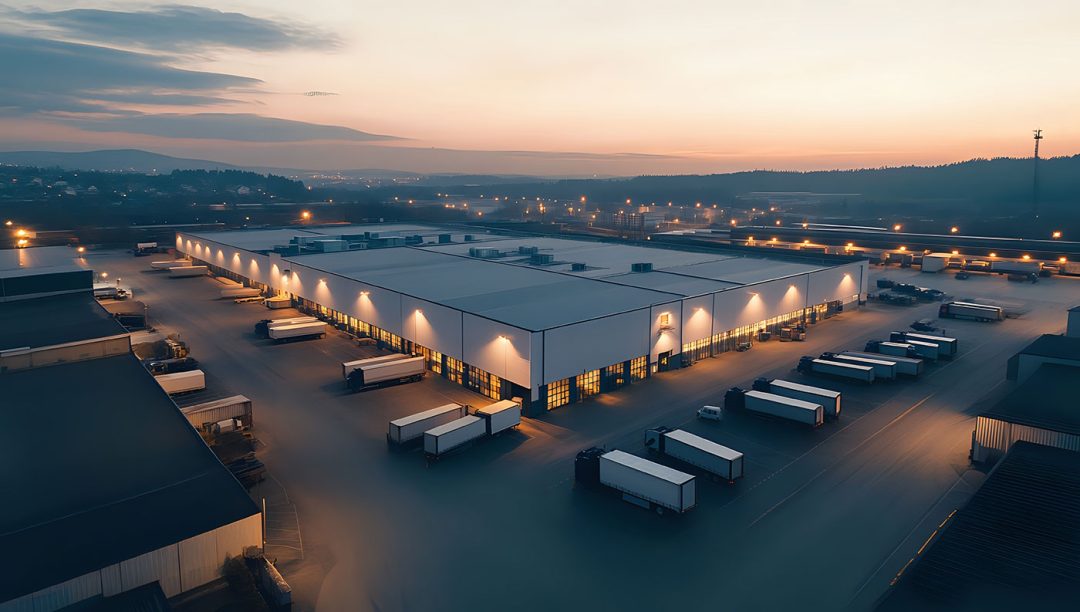
Increased Space Requirements:
Specific needs: Returns processing requires dedicated areas for unpacking, sorting, inspecting, and repackaging items. This can increase space needs by 20% or more compared to traditional forward logistics operations.
Buffer zones: Companies need extra space to handle fluctuations in return volumes, especially during peak seasons like post-holiday periods.
Example: A major clothing retailer might need to expand its 500,000 sq ft distribution center by an additional 100,000 sq ft just to handle returns efficiently.
Strategic Locations:
Urban proximity: There’s growing demand for facilities closer to city centers to reduce transportation costs and processing time for returns.
- Last-mile facilities: Small, urban warehouses are becoming popular for quick processing of returns and redeployment of items back into local inventory.
- Transportation hubs: Locations near airports, seaports, and major highway intersections are increasingly valuable for efficient reverse logistics.
- Example: Amazon has been acquiring and leasing smaller warehouse spaces in urban areas like New York City and Los Angeles specifically to handle returns and same-day deliveries.
- Specialized Facilities:
- Purpose-built design: New warehouses are being constructed with reverse logistics in mind, featuring larger receiving areas, flexible space configurations, and enhanced security measures.
- Refurbishment centers: Some companies are creating dedicated facilities for refurbishing and repackaging returned items, requiring specialized equipment and layout.
- Example: Best Buy has opened several standalone facilities dedicated to testing, repairing, and refurbishing returned electronics.
- Technology Integration:
- Smart warehouses: Advanced automation and robotics are being integrated into warehouse designs to handle the complexities of returns processing.
- IT infrastructure: Robust networks and data centers are needed to support sophisticated inventory management and tracking systems for returns.
- Example: Walmart has invested in AI-powered computer vision systems in some warehouses to quickly assess the condition of returned items and determine the best course of action.
- Environmental Considerations:
- Sustainability features: As companies focus on reducing waste from returns, warehouses are being designed with recycling facilities and energy-efficient systems.
- Example: Patagonia has incorporated extensive recycling and upcycling capabilities into its distribution centers to support its Worn Wear program for returned items.
- Multi-functional Spaces:
- Hybrid facilities: Some companies are creating spaces that combine traditional retail, e-commerce fulfillment, and returns processing.
- Example: Nordstrom has developed “Local” stores in urban areas that serve as service hubs for returns, alterations, and order pickups, blending retail and logistics functions.
- Cold Chain Logistics:
- Temperature-controlled facilities: With the growth of online grocery and meal kit deliveries, there’s increasing demand for cold storage facilities that can handle perishable returns.
- Example: HelloFresh has expanded its network of refrigerated warehouses to manage both outbound deliveries and potential returns of meal kits.
These factors are not only driving demand for new real estate but also influencing how existing properties are valued and renovated. Properties that can be easily adapted for efficient reverse logistics operations are seeing increased interest from both tenants and investors.
The cumulative effect is a reshaping of the industrial real estate landscape, with reverse logistics becoming a key consideration in property development, acquisition, and management strategies.